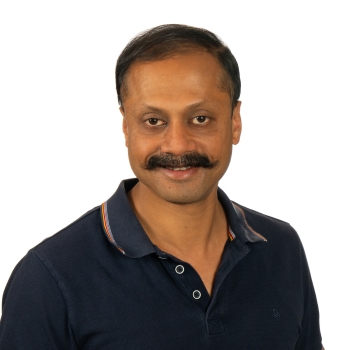
Indranil Brahma
About Indranil Brahma
Educational Background
- Ph.D. in Mechanical Engineering, University of Wisconsin-Madison, 2005
- M.S. in Thermal Engineering, Indian Institute of Technology-Delhi, 1998
- B.S. in Mechanical Engineering, National Institute of Technology-Kurukshetra, 1996
Research Interests
- Physics Informed Machine Learning
- Machine Learning based Measurement Technology
- Data driven modeling methods
- Internal combustion engines
- Particulate pollution and control
- Dynamic and pulsating flows
- Thermodynamics
Courses
- Machine Learning for Engineering Systems
- Thermal-Fluid System Design
- Senior Design Projects
- Heat Transfer
- Fluid Dynamics
- Thermodynamics
- Measurements
- System Dynamics
- Emission Control
Previous Work Experience
- Maruti-Suzuki Motor Corporation: Feb. 1997-May 2000, Automotive Engineering: Carburetors and Manual Transmissions
- Cummins Research and Technology: Feb. 2005-July 2009, Automotive Emission and Fuel Efficiency Research
Selected Publications
(Superscript ‘†’ indicates undergraduate student co-authors)
Brahma, I., & Singh, S. (2024). Experimental, numerical and deep learning modeling study of heat transfer in turbulent pulsating pipe flow. Applied Thermal Engineering, 122685.
Brahma, I. (2023). Using Long Short-Term Memory (LSTM) networks with the toy model concept for compressible pulsatile flow metering. Measurement, 223, 113782.
Brahma, I., & Ofili, O.† (2022). Nucleation-accumulation mode trade-off in non-volatile particle emissions from a small non-road small diesel engine. Environmental Science and Pollution Research, 29(59), 89449-89468. DOI: 10.1007/s11356-022-22032-w
Brahma, I. and Singh, S. (2021). Data-based Estimation and Simulation of Compressible Pulsating Flow with Reverse Flow through an Orifice. Flow Measurement and Instrumentation, 82, 102069.
DOI: https://doi.org/10.1016/j.flowmeasinst.2021.102069
Brahma, I., Jennings, R†., and Freid, B†. (2021). Using Physics to Extend the Range of Machine Learning Models for an Aerodynamic, Hydraulic and Combusting System: The Toy Model Concept. Energy and AI, 6, 100113. DOI: https://doi.org/10.1016/j.egyai.2021.100113
Brahma, I. (2019). Measurement and Prediction of Discharge Coefficients in Highly Compressible Pulsating Flows to Improve EGR Flow Estimation and Modeling of Engine Flows. Frontiers in Mechanical Engineering, 5, 25. DOI: https://doi.org/10.3389/fmech.2019.00025
Brahma, I.(2019). Extending the Range of Data-Based Empirical Models Used for Diesel Engine Calibration by Using Physics to Transform Feature Space. SAE Int. J. Engines 12(2):2019.
DOI: https://doi.org/10.4271/03-12-02-0014
Brahma, I. (2019). Measurement and Characterization of Flow Resistance of Critical and Near Critical Pulsating Flow through an Orifice Located in the Exhaust Stream of a Diesel Engine. SAE Int. J. Adv. & Curr. Prac. in Mobility 1(4):1604-1612, 2019. DOI: https://doi.org/10.4271/2019-01-1176.
Brahma, I. (2018). An alternative derivation of second law results to better relate derivation to practical exergy analysis. International Journal of Exergy, 25(4), 326-338.
DOI: https://doi.org/10.1504/IJEX.2018.091554
Brahma, I. (2014). Advantages and Applications of Transforming Empirical Model Input Space with Dimensional Models. International Journal of Engine Research, 15(7): pp. 877-894.
DOI: https://doi.org/10.1177/1468087414523420
Brahma, I., Schmidt, J.†, Confair, R. †, Kurtz, J. †, Rafter, I. †, Stryker, P. , and Johnson, D. (2014). An Investigation into the Accuracy of Orifice Based Flow Estimates for Pulsating Compressible Flows. SAE Int. J. Engines, 7(1): pp. 313-322, doi:10.4271/2014-01-1154.
DOI: https://doi.org/10.4271/2014-01-1154
Brahma I. (2014). Analysis and prediction of transient opacity spikes using dimensional modeling. International Journal of Engine Research, 15(3): pp. 263-81.
DOI: https://doi.org/10.1177/1468087413475807
Brahma, I. (2013). A decision-tree-based approach to smoke spike detection in a heavy-duty diesel engine. Proceedings of the Institution of Mechanical Engineers, Part D: Journal of Automobile Engineering, 227(8): pp. 1112-1129, DOI: https://doi.org/10.1177/0954407012464314
Brahma, I. (2012). Reduction of Transient Particulate Matter Spikes with Decision Tree Based Control. SAE International Journal of Engines, 5(2): pp. 608-621;
DOI: https://doi.org/10.4271/2012-01-0721
Brahma, I., & Chi, J. N. (2012). Development of a model-based transient calibration process for diesel engine electronic control module tables–Part 2: Modeling and optimization. International Journal of Engine Research, 13(2): pp. 147-168. DOI: https://doi.org/10.1177/1468087411424376
Brahma, I., & Chi, J. N. (2012). Development of a model-based transient calibration process for diesel engine electronic control module tables–Part 1: data requirements, processing, and analysis. International Journal of Engine Research, 13(1): pp. 77-96.
DOI: https://doi.org/10.1177/1468087411424377
Brahma, I. (2011). Development of Dynamic Constraint Models for a Model Based Transient Calibration Process. SAE International Journal of Engines, 4(1), pp. 813-827.
DOI: https://doi.org/10.4271/2011-01-0691
Brahma, I., Sharp, M.C., and Frazier, T.R. (2009). Empirical Modeling of Transient Emissions and Transient Response for Transient Optimization. SAE International Journal of Engines, 2(1), pp. 1433-1443. DOI: https://doi.org/10.4271/2009-01-1508
Brahma, I., Sharp, M. C., Richter, I. B., & Frazier, T. R. (2008). Development of the nearest neighbor multivariate localized regression modeling technique for steady state engine calibration and comparison with neural networks and global regression. International Journal of Engine Research, 9(4), 297-323.
DOI: https://doi.org/10.1243/14680874JER00708
Brahma, I., and Rutland, C.J. (2004). Optimization of Diesel Engine Operating Parameters Using Neural Networks. SAE Journal of fuels and Lubricants, Vol. 112, No. 4, pp. 2521-2529,
DOI: https://doi.org/10.4271/2003-01-3228
Patents
System for controlling an air handling system including an electric motor-assisted variable geometry turbocharger, US9528432B2, granted Dec 2016
System for controlling an air handling system including an electric pump-assisted exhaust gas recirculation, US9181905B2, granted Nov 2015
System and method for estimating engine exhaust manifold operating parameters US9778143B2, granted June 2015
System for controlling an air handling system including an electric pump-assisted turbocharger compressor, US8783030B2, granted July 2014
Fresh air flow estimation, US8677748B2, granted March 2014
System for controlling an air handling system including a dual-stage variable geometry turbocharger, US8567192B2, granted Oct 2013
Apparatus, system, and method for calibrating an internal combustion engine, US 7853395 B2, Date of Patent Dec 2010
Grant Awards
Acquisition of a Fast Particulate Spectrometer, National Science Foundation, Grant Number 1337929, PI, $166,240
Further Information
Contact Details
Location
224 Dana Engineering Building